Garments Costing:
Garments costing is an important factor in the garment export business. The whole business totally depends on it. Accurate costing can increase the growth of a business. For garments costing a merchandiser needs to have a clear conception of the raw materials price & Cost of Making the calculation of garments. The following factors are very important for garments costing. Here we will discuss the factors considered before garments costing.
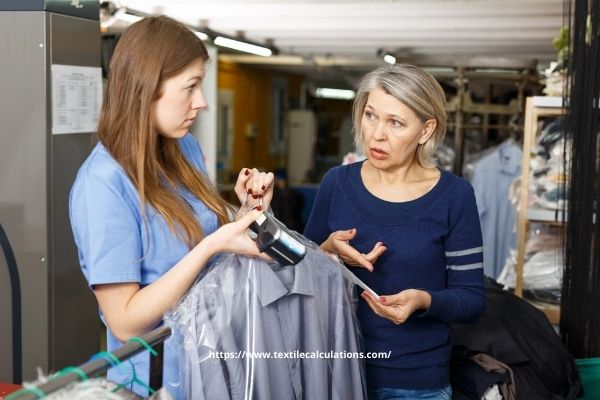
Factors Considered Before Garments Costing:
- Fabrication: You must take a clear idea regarding the fabrication before taking the order from the buyer/buying house. After then, you must ensure that you have a strong source of the following fabric.
- Size spec: Make sure that, you have got the correct/latest size spec with the measurement of all the sizes, which will be ordered. Many times we see that PO sheet has come with a new bigger size which was not during the costing.
- Fabric color: Try to know that, how many colors the style has & also try to know that, color-wise order qty ratio.
- Qty: Take information regarding approximate order qty.
- Shipment date: Asked buyer for the shipment date & check with your production department that, they have enough space for shipped out the following qty within the required ship date Or tell your possible date.
- Test requirement: Let you know that, the order has any test or not.
- L/c payments term: Take a previous l/c copy from them & discuss with your commercial people regarding all the terms along with payment terms.
- Inspection: Pls get a confirmation from the buyer that, who will inspect the goods. If third party then who will pay their charges.
- GSP: Pls confirm the buyer has needed the GSP or not.
- Price: Price mainly depends on shipping line FOB, C&F, CIF.
- Print: If the garments have print then make sure that you have a clear artwork of them. Check that there clearly mentioned the print quality, dimension & placement. Send the artwork to your printers for a better price idea. Also, let you know from your printers regarding the difficulties of the following print. Many times we found that buyer has asked for so many types/kinds of prints in the same body which is so difficult for production. Such as, if the buyer asked for Flock + discharge & foil print in the same artwork then it is not possible for production.
- Embroidery: Discuss with your embroidery supplier regarding the embroidery & take price quotation.
- Wash: Take the wash price quotation from the washing factory.
- Test: Confirm the charges of the test from the testing company.
Accessories & trims:
Pls, try to Calculate the price of accessories individually it will reduce your percentage of mistakes. Pls find below the list of some accessories items.
- Sewing thread: Confirm that, which thread you need 100% cotton, spun polyester, or filaments. Then ensure the count 50/2 or 40/2 or any other denier. It may vary on fabrications. Regarding the pigment dye garments we normally used cotton grey color cotton thread. Calculate the sewing thread consumption part by part & add require wastage percentage.
- Labels: Take the quotation from your supplier for the entire woven & satin/paper label.
- Tape: Calculate the consumption of tape if it has, such as Velvet, herringbone or canvas, etc.
- Elastic: Make sure which denier & width it needs. Then take the quotation from the supplier.
- Zipper: If the garments have zippers then confirm that, from where you will purchase that. Many times the logo zipper need to import the mold from abroad. Make sure the zipper quality, such as metal, nylon or vision zipper. Check the zipper measurement from your production department and get prices from your zipper supplier.
- Button: Take the button price from your supplier if the garments have it.
- Interlining: Calculate the interlining price if the garments need.
- Patch or badge: Calculate the patch or badge or another metal item if the garments have.
- Finishing item: Tissue paper, silica gel, hangtag, barcode sticker, backboard, h/tag string, scotch tape, security tag calculate the prices of this item.
- Hanger: Take the quotation of the hanger.
- Poly: Make the measurement of poly. Confirm the quality & with adhesive or not.
- Carton: Find out the carton measurement & take the prices from the carton supplier along with top, bottom & divider.
- Gum tape: Confirm the gum tape quality that, whether it is normal transparent or with any logo. Then take the price quotation.
- PP belt: Take the price quotation of pp belt if the buyer asked it.
- Carton sticker: Take quotation for a sticker.
- Commercial cost: Normally we add 3% of total purchase (Fabric cost+ other item cost + Accessories cost) as commercial cost if the L/c payments terms are as sight. If the l/c is 60 days deferred then you can add 7.5% additional cost of the total price and it will be 15% for 90 day deferred.
- CM (Cost of making): Calculate the CM after discussion with your production department. It varies depends on require machine qty & output qty.
- Profit: Normally we add 20% of CM cost with the price as profit.
Cost Calculation System:
- During the fixation of price following notes are to be followed carefully:
- Cost of fabric /Doz
- Cost of accessories /Doz.
- Garments C. M (Cost of manufacturing)/Doz. Garments
- Cost of transportation from factory to seaport or airport.
- Clearing & forwarding cost
- Overhead Cost.
- Commission/Profit.