Introduction
Carding is a mechanical process that disentangles, clean and intermixes fibers to produce a continuous web or sliver suitable for subsequent processing. This is achieved by passing the fibers between differentially moving surfaces covered with card clothing. In carding, fibers are opened to more or less single fibers. Dust, dirt, small trash particles, nep and other impurities are removed here. Fiber blending and parallelization are also done here. That’s why Carding is called “Heart of Spinning”. Calculations play an important role during the carding process. Some important production calculations (with example) of carding machine and process are mentioned in the following article.
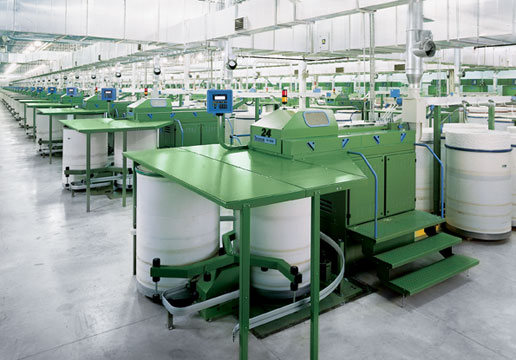
Some Important Conversion Factors for Carding Machine Production Calculations:
- 36 inch = 1 Yard;
- 1 Lea = 120 Yards;
- 1 Meter = 1.0936 Yards;
- 1 Pound (lb) = 453.6 Gram = 16 Oz
- 840 Yard = 7 Lea = 1 Hank;
- 1 Pound (lb) = 7000 Grains;
- 1 Meter = 39.37 Inch;
- 1 KG = 2.205 Pound (lb)
Hank or count means the number of 840 yards length that weight exactly 1 pound (lb)
Card sliver hank ranges 0.12, 0.13; 0 12 means 0.12 x 840 yards in 1 pound of sliver.
Carding Machine Efficiency, Wastage, Draft & Production Calculations:
…………………………………..Delivery Hank
1. Draft or Actual Draft = —————————–
……………………………………..Feed Hank
…………………………………………..L x w
2. Feed Hank or Lap Count = —————-
…………………………………………..l x W
Example: Find the draft of carding machine if lap weight 500 gm/m and sliver hank = 0.122.
Solution:
…………..Delivery Hank
Draft = ————————–
……………Feed Hank
………………………………………L x w
Feed hank or Lap count = ————–
………………………………………l x W
Here, W = 500 gm/m
…..500 x 0.9114
= ———————
……….453.6
= 1.0046 lbs/yard
So, L = 1 Yard
w = 1 lb
l = 840 yard
………………………………………L x w
Feed Hank or Lap Count = ————
………………………………………l x W
……….1 x 1
= ————————-
….840 x 1.0046
= 1.185 x 10-3 Ne
Here, Delivery Hank = Sliver Hank = 0.122
…………Delivery Hank
Draft = ————————-
………….Feed Hank
……….0.122
= ——————— = 1.02 (Ans)
…..1.185 x 10-3
……………………….Mechanical Draft
3. Actual Draft = ——————————— x 100
…………………………100 – Waste%
Example: Find the actual draft of a carding m/c for mechanical draft = 86, waste extraction = 7%, Lap hank is 0.0012, what will be sliver hank?
Solution:
Here, Mechanical draft = 86
Waste% = 7
…………………..Mechanical Draft
Actual Draft = ————————— x 100
…………………….100 – Waste%
…….86
= ———– x 100 = 92.47 (Ans)
….100– 7
Here, Feed hank = Lap hank = 0.0012
……………………..Delivery Hank
Actual Draft = ————————-
………………………Feed Hank
Or, Delivery hank= Actual draft x Feed hank
= 92.47 x 0.0012
= 0.1109 (Sliver hank) (Ans)
……………………………..Surface Speed of Delivery Roller
4. Mechanical Draft = —————————————————————
………………………………..Surface Speed of Feed Roller
Example: A Carding m/c running with following:
- RPM of Feed Roller = 2
- RPM of Delivery Roller = 10
- Dia of Feed Roller = 2.3”
- Dia of Delivery Roller = 27”
Find out mechanical draft?
Solution:
……………………………..Surface Speed of Delivery Roller
Mechanical Draft = ——————————————————–
………………………………..Surface Speed of Feed Roller
….π x RPM of Delivery Roller x Dia of Delivery Roller
= ———————————————————————————–
……..π x RPM of Feed Roller x Dia of Feed Roller
….3.1416 x 10 x 27
= ————————- = 58.69 (Ans)
….3.1416 x 2 x 2.3
………………………………………..Total Working Mins – Total Stoppage Mins
5. Carding Machine Effi.(%) = ———————————————————————x 100
………………………………………………………..Total Working Mins
Example: Calculate the carding machine efficiency (%) using the following data-
- Sliver breakages = 10 Mins
- Stoppage due to can changes = 25 Mins
- Cleaning & other stoppages = 20 Mins
- Total working time = 8 hrs = 480 Mins
Solution:
Total Stoppage Time = Sliver breakages + Stoppage time due to can changes + Cleaning & other Stoppages
= 10 + 25 + 20 = 55 Mins
………………………480 – 55
Efficiency (%) = —————–x 100 = 88.5% (Ans)
…………………………480
…………………………………π x Doffer Dia x Doffer Speed x Efficiency x 60 x 24
6. Production per Day = —————————————————————————————
………………………………………………………36 x Sliver Hank x 840
Example: A carding spinning mill has 10 cards. It runs; find out the production per day in kg from the following data-
- Delivery speed = 200 m/min
- Doffer dia = 27”
- Delivery sliver weight = 70 grains/yard
- Card efficiency = 95%
- Dia of feed roller = 2.25”
Solution:
Here, Delivery sliver weight, W = 70 grains/yard
= 70/7000 = 0.01 lbs/yard
L = 1 Yard
w = 1 lb
l = 840 Yard
………………….L x w
Sliver hank= —————-
………………….W x l
…….1 x 1
= —————-
…0.01 x 840
= 0.119 Ne
Here,
- Card efficiency = 95% = 0.95
- Doffer dia = 27”
- Doffer speed = 200 m/min
- Sliver hank = 0.119 Ne
- No of Cards = 10
……………………………………….3.1416 x 27 x 200 x 1.0936 x 0.95 x 60 x 24 x 10
Production per day in kg = ———————————————————————————
………………………………………………………..36 x 0.119 x 840 x 2.205
= 31985.4 kg/day (Ans)
……………………..Surface Speed of Doffer (inch/min) x 60 x 24 x Tension Draft
7. Production/Day = ——————————————————————————————–
…………………………………………………….36 x Sliver Hank x 840
…………………………………………….Sliver Length x Unit weight
8. Sliver hank or Sliver count = —————————————————–
…………………………………………….Sliver Weight x Unit Length
Example: Find out production per day in modern carding m/c-
- Doffer speed = 10 RPM
- Doffer dia = 27”
- Delivery sliver weight = 68 grains/yard
- Efficiency = 95%
- Waste = 3%
- Tension draft = 1.1
Solution:
Here, Delivery sliver weight, W = 68 grains/yard
= 68/7000 = 0.0097 lbs/yard
L = 1 Yard
w = 1 lb
l = 840 Yard
……………………………………………..Sliver Length x Unit weight
Sliver hank or Sliver count = —————————————————–
……………………………………………Sliver Weight x Unit Length
……..1 x 1
= ———————-
…0.0097 x 840
= 0.122 Ne
Surface speed of doffer = π x Doffer speed (rpm) x Doffer dia (inch)
= 3.1416 x 10 x 27
= 848.232 inch/min
Here, Tension draft = 1.1
Efficiency = 95% = 0.95
Waste = 3% = (100-3)/100 = 0.97
…………………………..Surface Speed of Doffer x 60 x 24 x Efficiency x Waste x Tension Draft
Production Per Day = —————————————————————————————————–
……………………………………………………………….36 x Sliver Hank x 840
….848.232 x 60 x 24 x 0.95 x 0.97 x 1.1
= ———————————————————- lbs
………………36 x 0.122 x 840
= 335.6 lbs (Ans)
……………………………………..Sliver Weight (kg) x 36 x 840 x Sliver Hank x 2.205
9. Time Reqd. to Fill 1 Can = ——————————————————————————
………………………………………..π x Doffer Speed x Doffer Dia x Efficiency
Example: Weight of Empty can = 6 kg; wt. of Pull can = 14kg Sliver Hank = 0. 14, Doffer dia = 27”, Doffer speed = 18 RPM, Efficiency = 80%; Time required to fill one can =?
Solution:
Here,
Sliver Weight = Full Can wt. – Empty Can wt. = 14-6=8 kg.
Doffer Speed = 18 rpm
Doffer Dia = 27”
Efficiency = 80% = 0.8
Sliver Hank = 0.14
……………………………………………………….8 x 36 x 840 x 0.14 x 2.205
Time Requirement to Fill One Can = ————————————————– Min
…………………………………………………………..3.1416 x 18 x 27 x 0.8
= 61.14 Min (Ans)
…………………………………………………..Sliver Weight (lb) x 36 x 840 x Sliver Hank
10. Time for A Card to Exhaust A Lap = —————————————————————
……………………………………………………….π x Doffer Speed x Doffer Dia x Effi.
Example: Calculate the time taken for a card to exhaust a Lap with following data. Lap weight = 35lbs; Sliver Hank = 0. 16; Efficiency = 85 %, Waste = 1 lb, Doffer dia = 27″, Doffer speed = 10 RPM.
Solution:
Here, Sliver weight = (lap wt.- waste) =35-1= 34 lbs
i.e., Production of the sliver from 35 lbs lap is 34 lbs.
Doffer dia = 27”
Doffer speed = 10 rpm
Sliver hank = 0.16
Efficiency = 85% = 0.85
…………………………………………………………………34 x 36 x 840 x 0.16
Time Taken for A Card to Exhaust A Lap =—————————————— Mins
………………………………………………………………3.1416 x 10 x 27 x 0.85
= 228 Mins or 3 Hour 48 Mins (Ans)
………………………………………Trash in Lap – Trash in Sliver
11. Cleaning Efficiency (%) =————————————————– x 100
………………………………………………….Trash in Lap
Example: Calculate the cleaning efficiency after carding process. Trash in Lap = 3.75% & Trash in sliver = 1.25%.
Solution:
Trash in Lap = 3.75% = 0.0375
Trash in Sliver = 1.25% = 0.0125
……………………………..Trash in Lap – Trash in Sliver
Cleaning Efficiency = ——————————————— x 100
……………………………………….Trash in Lap
…0.0375 – 0.0125
= —————————– x 100
………0.0375
= 66.67 % (Ans)
………………………………………….Wastage Weight
12. Carding Wastage% = ———————————————— x 100
……………………………………Wastage wt. + Sliver wt.
Example: Calculate the wastage% using the following data-
Empty Can Weight = 13 kg
Sliver + Can Weight = 25 kg
Wastage Weight = 678 gram = 0.678 kg
Solution:
Sliver weight = (Sliver + Can weight) – Empty Can Weight
= 25 – 13 kg = 12 kg
………………………….Wastage Weight
Wastage% = ——————————————– x 100
…………………..Wastage wt. + Sliver wt.
……..0.678
= —————– x 100 = 5.35% (Ans)
…0.678 + 12
13. Nep Count, n = No. of nep per inch 2 card web (m) x 100
Example: A 42” wide card web of multiplying 100 of the mean value per square inch. Calculate the nep count of that card web?
Solution:
For calculating the nep count, at first a web is collected from the card and placed on a 10” x 10” black board. Then the neps are counted and the number of neps found is corrected for any difference in hank.
Nep count, n = m x 100 = 0.13 x 100 = 13 (Ans)
Conclusion
I have tried to explain the production formulas with examples of different calculations of carding machine through this article. Hope this article will be helpful for those who are new to the factory or those who are students.
Author of this Article:
Md. Imran Hossain
B.Sc. in Textile Engineering
Shahid Abdur Rab Serniabat Textile Engineering College, Barisal.
Email: [email protected]
You may also like: